BESCHICHTUNGEN UND GLEITLACKE
BESCHICHTUNGEN UND GLEITLACKE
SCHUTZ VOR VERSCHLEIß,
REIBUNG UND KORROSION
PTFE-Beschichtungen und andere Kunststoffbeschichtungen verbessern die Oberflächeneigenschaften von Bauteilen oder schützen sie vor äußeren Einflüssen.
Beschichtungen mit Festschmierstoffen dienen als Trockenschmierung und ersetzen daher meistens herkömmliche Schmierstoffe wie Fett oder Öl. Sie reduzieren die Reibungskräfte der Bauteile während der Montage oder im dynamischen Einsatz und schützen die Teile vor Montagebeschädigungen oder starkem Verschleiß. Farbige Beschichtungen kennzeichnen darüber hinaus Kleinteile für eine spätere Qualitätskontrolle.
Beschichtungen für Elastomerteile sind ebenso wie das Basismaterial elastisch und haften daher selbst bei Dehnung fest auf dem Bauteil.
Kunststoffbeschichtungen mit speziellen Additiven wirken als Korrosionsschutz für Metallteile. Sie bilden einen durchgängigen Überzug und schirmen die Oberflächen der Metalle gegen korrosive Gase oder Flüssigkeiten ab.
GLEITLACK ODER PTFE BESCHICHTUNG?
GLEITLACK ODER PTFE BESCHICHTUNG?
Im allgemeinen Sprachgebrauch sind unterschiedliche Bezeichnungen für reibungsreduzierende Beschichtungen üblich. Hersteller sprechen oft von Gleitlacken. Anwender dagegen nutzen gerne Begriffe wie beispielsweise PTFE-Beschichtung, Teflon-Beschichtung*, PU-Beschichtung bzw. Polyurethanbeschichtung, Kunststoffbeschichtung oder eben einfach nur den allgemeinen Ausdruck Beschichtung. Gemeint ist im Regelfall dasselbe. Es geht um Lacke, die flüssig auf die Bauteile aufgetragen werden, dort aushärten und eine trockene, fest anhaftende, eventuell dehnbare Funktionsschicht bilden.Die Bezeichnungen Gleitlack, Beschichtung oder Kunststoffbeschichtung können dabei als Überbegriffe betrachtet werden. Begriffe wie PTFE-, Teflon- oder PU-Beschichtungen beschreiben jedoch Lacke mit definierten Inhaltsstoffen.
*Teflon™ ist eine Handelsmarke von The Chemours Company FC, LLC, ehemals DuPont. Die Bezeichnung Teflon wird umgangssprachlich oftmals synonym für PTFE verwendet.
FUNKTIONSWEISE VON GLEITLACKEN
FUNKTIONSWEISE VON GLEITLACKEN
Gleitlacke werden in unterschiedlichen Verfahren flüssig auf die Bauteile aufgebracht und härten dort aus. Sie bilden auf den Oberflächen der Bauteile eine sehr dünne, gleichmäßige, trockene und meistens elastische Schicht. Im Gegensatz zu Öl, Fett oder Pulvern haften Gleitlacke fest auf den Oberflächen und erfüllen größtenteils dauerhaft ihre schmierende und schützende Funktion. Sie können als alleinige Schmierung oder aber in Kombination mit Ölen oder Fetten eingesetzt werden.WARUM WIRD BESCHICHTET?
WARUM WIRD BESCHICHTET?
Beschichtungen dienen meistens als Montagehilfe oder optimieren die Gleiteigenschaften der Bauteile im dynamischen Einsatz. Häufig werden sie auf O-Ringe und andere Dichtungen aufgebracht und schützen die Dichtelemente vor Montageschäden oder übermäßigem Abrieb. Farbige Beschichtungen kennzeichnen die Bauteile und sorgen so für eine zuverlässige Qualitätskontrolle. Beschichtungen sorgen dafür, dass Ventile nicht an den Dichtungen verkleben und verhindern Stick-slip-Effekte, also das Ruck-Gleiten der Elemente. Reibkräfte lassen sich auf diese Weise generell reduzieren und die Geräuschentwicklung, ausgelöst durch Reibung, teilweise ganz eliminieren.WAS WIRD BESCHICHTET?
WAS WIRD BESCHICHTET?
Gleitlacke werden in unterschiedlichen industriellen Anwendungen eingesetzt. Je nach Lack und Zielsetzung können Kunststoffe (Thermoplaste), Elastomere oder Metalle beschichtet werden. Die Beschichtungen werden häufig für O-Ringe und andere Dichtungen, Dämpfer, Schrauben, Federn, Klemmen, Schalter und sonstige Funktionsteile eingesetzt.
Gleitlacke bzw. Beschichtungen sind Stoffgemische aus organischen oder anorganischen Bindemitteln, Festschmierstoffen, Lösungsmitteln und unterschiedlichen Additiven. Je nach Zielsetzung unterscheiden sich die Festschmierstoffe und Additive.
AUFBAU VON
GLEITLACKEN
UND BESCHICH
TUNGEN
Bindemittel
Die Basis von Gleitlacken sind organische oder anorganische Binder. Je nach Gleitlack, Hersteller und Zielsetzung kommen dabei unterschiedliche Substanzen zum Einsatz. So können die Beschichtungen auf Epoxidharzen, Polysiloxanen, Polyurethan oder anderen Kunststoffverbindungen basieren.
Der Festschmierstoff
Der bekannteste Festschmierstoff, der in Gleitlacken zum Einsatz kommt, ist derzeit PTFE. Daher wird häufig von PTFE-Beschichtungen gesprochen, obwohl es durchaus noch andere funktionelle Beschichtungssysteme gibt. Neben PTFE (Polytetrafluorethylen) werden beispielsweise auch Molybdändisulfid (MoS₂), Graphit oder Kombinationen aus unterschiedlichen Festschmierstoffen eingesetzt. PTFE als Festschmierstoff steht seit Anfang 2023 zur Diskussion, nachdem die ECHA (European Chemicals Agency) einen allgemeinen REACh-Beschränkungsvorschlag für PFAS (Per- und Polyfluoralkylsubstanzen) veröffentlicht hat.
Die Additive
Je nach Einsatzzweck werden den Gleitlacken noch verschiedene funktionelle Additive beigemischt. Dies können Korrosionsschutzmittel, UV-Indikatoren, Farbpigmente und andere Substanzen sein.
Die Lösungsmittel
Lösungsmittel, welcher Art auch immer, sind für die Herstellung und Verarbeitung der Gleitlacke essentiell. Obwohl es noch zahlreiche Gleitlacke auf Basis flüchtiger, organischer Lösemittel am Markt gibt, werden speziell für Elastomere und Kunststoffe immer mehr Beschichtungen auf Wasserbasis hergestellt. Im Zuge des Umwelt- und Gesundheitsschutzes gilt auch bei der Gleitlackproduktion und -verarbeitung die Devise, Gefahrenstoffe zu vermeiden. Daher wurden während der letzten Jahre auch die sogenannten NMP (N-Methyl-2-pyrrolidon) Co-Lösemittel aus den Gleitlacken verbannt.
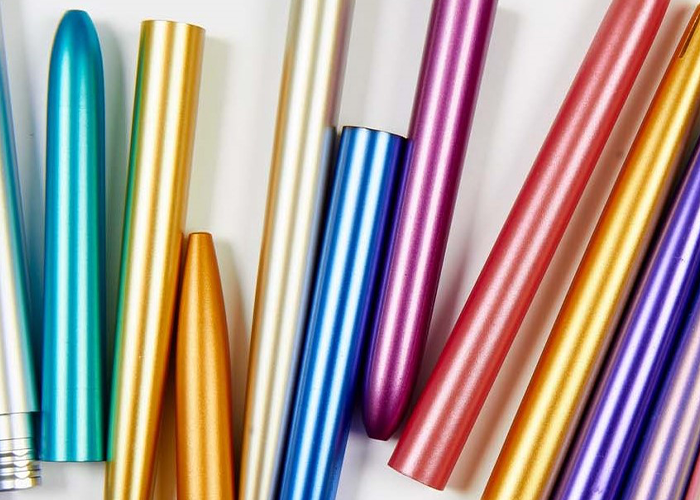
EINSATZ
BEREICHE UND
VARIANTEN
Mit zunehmender Automatisierung in der Fertigung und Montage finden funktionelle Beschichtungen einen immer breiteren Einsatz in industriellen Anwendungen. Sie bieten eine saubere Lösung, belastete Maschinenelemente, insbesondere Elastomerteile dauerhaft zu schmieren, erhöhen damit deren Lebensdauer und erleichtern die Montage von Kleinteilen. Werden die Gleitlacke in automatisierten Batch-Verfahren aufgetragen, so können Anwender sich darauf verlassen, dass alle Bauteile beschichtet sind.
Je nach Zusatzstoffen gibt es Beschichtungen u.a. für folgende Anwendungsbereiche und Kleinteile:
Für den Lebensmittel- und Trinkwassereinsatz sind die entsprechenden Zulassungen der DVGW, NSF, FDA oder der Verordnung (EC) 1935/2004 notwendig. Die häufig enthaltenen UV-Indikatoren sind in diesem Fall nicht zulässig, Farbpigmente nur mit passender Zulassung bzw. Konformität.
LABS-konforme Qualitäten sind erhältlich, setzen jedoch ein passendes Basismaterial des Bauteils, LABS-konforme Lacksysteme und geeignete Beschichtungs- und Reinigungsprozesse voraus.